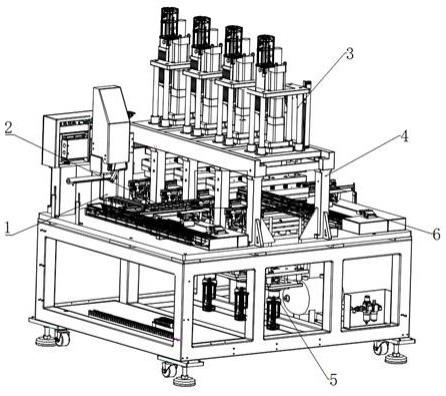
1.本发明属于液压压合设备技术领域,具体涉及一种基于基板保压的液压式保压工装及保压系统。
背景技术:2.由于半导体基本内部电路的独特设置,在进行蚀刻后,需要对成型的芯片进行封装,封装时,需要借助保压装置将内部成型的半导体进行完全封装,以便达到生产使用需要,由于芯片半导体本身的结构较为精密,因此在进行每一步的环节要求都较高,特别是对于保压环节的温度以及压力的控制极高,一但出现偏差就会影响整个基板的保压封装工序。
3.在申请号为cn201921643661.0中公开了一种半自动保压设备,在该装置中,包括:控制柜;控制器,装设于控制柜内;设备通过保压气缸将注胶后的待保压产品通过特定的保压腔室将其压住,从而避免了注胶后的反弹,既保证了产品的高度要求,又保证了粘胶面积。
4.但是该装置虽然实现了在装置结构上能够实现采用保压气缸对基板的保压作业,但是该结构制作是对于保压的精度以及时间或精度控制完全无法达到生产需要,会造成保压时的良品率极低。
5.同时在中国专利申请号为2022109235269中公开了一种含压力反馈的自重压合装置及压合系统,这种自重压的压合方式是采用自重压模组的自身配重对位于载具上的基板进行压合,但是由于自重压模组采用的是自身重量对基板进行压合,这种压合方式完全是靠砝码本身的重量,最多才能达到几十千克的重量压力,在一些特定基板上的应用会受到局限,甚至还会造成良品率降低。
技术实现要素:6.针对现有技术的不足,本发明的目的在于提供一种基于基板保压的液压式保压工装及保压系统,解决了现有技术中存在的上述技术问题。
7.本发明的目的可以通过以下技术方案实现:一种基于基板保压的液压式保压工装,包括上料检验模组、流水带机构、液压压合模组、支撑轨道、顶升模块、下料检验模组,所述上料检验模组包括上料接驳单元及上料检验单元,通过上料接驳单元将贴盖基板的载台输送至上料检验单元检测;所述流水带机构包括固定支架、传送组件,通过传送组件将承载有基板的载台传输至液压压合模组所在的下方并定位;所述液压压合模组包括液压组件、支撑板、压力传感器、压感组件、压头,所述液压组件设置于支撑板所在的上方位置,并通过液压组件对位于下方的压感组件进行施压,位于压感组件下表面设置有向下突出的压头,所述压力传感器设置于液压组件所在的下方位置,通过压力传感器感应液压组件下压时的压力并反馈给控制中心,通过压感组件的自加
热实现对位于下方的压头同步升温;所述支撑轨道用于对液压压合模组上的支撑板进行支撑,同时顶升模块位于支撑轨道所在的下方位置;所述顶升模块包括伺服电机、丝杆组件、顶升面板,所述伺服电机通过丝杆组件连接在顶升面板上,通过丝杆组件在上下方向的驱动实现对顶升平台的顶升和下降,所述顶升面板从流水带机构所在的载台上将阵列分布的贴盖基板顶升抬起,同时位于液压压合模组上的压头向下对贴盖基板进行下压;所述下料检验模组用于对保压工序完成的载台上的基板进行转运。
8.进一步的,所述液压组件所在的侧边设置有光栅尺,通过光栅尺所在的刻度标识对液压组件的下降间距进行记录并标记,同时反馈给控制中心。
9.进一步的,位于所述液压组件在竖直方向同步设置有若干组导向杆,使导向杆贯穿支撑板并与下方的压感组件连接,用于对液压组件的竖直方向运动起平衡导向作用。
10.进一步的,所述压力传感器所在的下方与矩形弹簧座连接,同时使压力传感器位于平四角位置,用于感应位于液压组件的下压压力,实现压力平衡感应。
11.进一步的,所述压感组件包括加热板、隔热板、平衡板,所述加热板位于下方,并通过隔热板与上方的平衡板连接并形成整体;所述加热板通过电加热方式对压头整体进行加热。
12.进一步的,所述平衡板所在的上端面设置有平衡调节阀,通过平衡调节阀用于对平衡板进行水平度调节。
13.进一步的,所述压头设置有若干组,并置于block板所在的下端面,并保持压头所在的下端面整体保持水平平衡;所述block板整体嵌装在压感组件的加热板下端面上,并通过加热板的加热传导带动block板的传导。
14.进一步的,所述block板所在的下端面竖直方向设置有若干组销钉,使销钉对压头形成外周的包围,同时销钉向下伸出的高度大于压头本身的厚度;使block板与流水带机构上的载台接触时,销钉对载台整体产生向下的挤压压力,并同步操作顶升模块的顶升实现位于载台上的贴盖基板向上抬升,直至压头与贴盖基板的上端面接触。
15.进一步的,所述销钉位于block板所连接的端部设置有减震弹簧件,使销钉受压时同步实现收缩,脱离时同步实现回弹。
16.所述的基于基板保压的液压式保压工装的保压系统,包括以下步骤:s1、通过上料检验模组将贴盖基板的载台进行视觉检测后转运至流水带机构上;s2、通过流水带机构的传送组件将载台转运至液压压合模组所在的下方,随后通过流水带机构对载台所在的四周方向进行限位固定;s3、控制所述液压压合模组对位于载台上承载的贴盖基板进行上端面的压合作业,位于液压压合模组上的压力传感器同步记载压合压力并反馈给控制中心,同时所述顶升模块向上顶升,使得顶升面板从载台所在的下端面对贴盖基板进行顶升作业;s4、通过流水带机构将完成保压的贴盖基板及载台整体转移至下料检验模组上,通过下料检验模组将贴盖基板重新检测后,再转运至下一个工序。
17.本发明的有益效果:1、本装置采用的液压压合模组从顶部向下进行液压压合作业,可实现1000kg的大压力对贴盖基板进行压合作业,保证贴盖基板在进行保压压合时的温度以及压力均满足精度要求,提高其整体的良品率,并降低运营和检测成本上。
18.2、本装置的所采用的光栅尺能给基于指定的刻度标识,以便液压组件在达到指定的液压挤压刻度时,并保持指定的保压时间,达到生产需要,操作完成后,再进行复位了为下一个工序做准备。
19.3、本装置位于压感组件所在下端面设置有独立的block板,并实现block板与压头形成一体,该结构能够实现快速更换提到,满足不同的贴盖基板保压需要。
附图说明
20.为了更清楚地说明本发明实施例或现有技术中的技术方案,下面将对实施例或现有技术描述中所需要使用的附图作简单地介绍。
21.图1是本发明实施例的整体结构示意图;图2是本发明实施例的俯视结构示意图;图3是本发明实施例的正面整体结构示意图;图4是本发明实施例的上料模组结构示意图;图5是本发明实施例的流水带机构结构示意图;图6是本发明实施例的液压压合模组整体结构示意图;图7是本发明实施例的图6中a处部分结构示意图;图8是本发明实施例的液压压合模组正面结构示意图;图9是本发明实施例的图8中b处部分结构示意图;图10是本发明实施例的支撑轨道结构示意图;图11是本发明实施例的顶升模块连接状态结构示意图。
具体实施方式
22.下面将结合本发明实施例中的附图,对本发明实施例中的技术方案进行清楚、完整地描述。基于本发明中的实施例,本领域普通技术人员在没有作出创造性劳动前提下所获得的所有其它实施例,都属于本发明保护的范围。
23.如图1、图2、图3所示,本发明实施例提供一种基于基板保压的液压式保压工装,包括上料检验模组1、流水带机构2、液压压合模组3、顶升模块5、下料检验模组6,位于外部通过罩壳封盖(起到防尘作用),如图4所示,上料检验模组1包括上料接驳单元11及上料检验单元12,通过上料接驳单元11将贴盖基板的载台101输送至上料检验单元12检测;上料检测单元12包括检测相机121、驱动组件122、支座123,支座123位于上料检验模组1所在的端部位置,通过驱动组件122实现检测相机121的位置调整,检测相机121对承载有贴盖完成的贴盖基板进行视觉检测,检测在热压之前的贴盖基板上的贴盖是否发生偏移;横向移动采用驱动组件122的直线传输方式进行驱动,保证拍摄效果的稳定(具体的使用方法可参照申请号为2022108308405的专利)。
24.如图5所示,流水带机构2包括固定支架21、传送组件22,固定支架21用于支撑固
定,传送组件22,侧边的电机作为驱动源驱动,即当载台101接触到两侧设置的传送组件22时,则此时在摩擦力的作用下,传送组件22会对载台101整体进行传输,随后位于固定支架21所在前端部设置有限位组件221,该结构阻挡了载台101的继续传输(载台101被运送至指定位置时,即液压压合模组3所在的正下方,位置精度可进行调节),随后位于固定支架21所在的后端部设置有另一组限位组件221被抬升,对载台101实现在传输的左右两个方向的限位夹持(后端部另一组限位组件221为上下方向的伸缩式结构设置,当载台101开始传输时处于收缩状态,不影响载台101的传输,当传输至前端部的限位组件221被限位后会被抬升,从而从前后两个方向限制载台101的位置),同时位于固定支架21所在的侧边设置有定位组件211,当载台101运动被限位传输方向被限位时,会从侧边对载台101的位置进行固定,从而保证位于载台101在4个侧面方向(即定位组件211以及前后两个限位组件221为三个方向,固定支架21本身所在的一边共同围成四个侧边)的固定,保证了定位的精准,此时的载台101被传输至液压压合模组3所在的下方。
25.同时固定支架21所在的侧边位置设置有翘边检测组件212,通过翘边检测组件212对传输至固定支架21前端部位置的载台101进行翘边检测,防止有翘边的贴盖基板产品进行保压,而损伤贴盖基板产品。
26.如图6、图7、图8、图9所示,液压压合模组3包括液压组件31、支撑板32、压力传感器33、压感组件34、压头35,此时的支撑板32位于液压压合模组3整体所在的中部位置,液压组件31设置于支撑板32所在的上方位置,其他组件位于支撑板32所在的下方位置,并通过液压组件31对位于下方的压感组件34进行施压,液压组件31所在的侧边设置有光栅尺312,通过光栅尺312所在的刻度标识对液压组件31的下降间距进行记录并标记,此时的光栅尺312采用电控控制并连通,开始时设定指定压力(即光栅尺312根据设定值标定有一个预设压力),当驱动液压组件31下压时,达到光栅尺312所标定的预设压力即停止下压,并根据程序保压指定时间,随后液压组件31完成复位,并将保压压力以及保压结果反馈给控制中心。
27.为了提高液压组件31下压时的稳定性(此时液压组件31的压力最大可达到1000kg),会在液压组件31下压的竖直方向同步设置有导向杆311(丝杆组件311可保证移动精度
±
5μm),使导向杆311贯穿支撑板32并与下方的压感组件34连接,用于对液压组件31的竖直方向运动起平衡导向作用。
28.压力传感器33所在的下方与矩形弹簧座331连接,矩形弹簧座331隔绝了加热状态的压感组件34对压力传感器33的影响,保证压力传感器33的工作稳定性。同时使压力传感器33位于平四角位置,用于感应位于液压组件31的下压压力,实现压力平衡感应后再下压,保持位于下端面的压头35总受压保持一致且平衡。压力传感器33将在保压状态下的压头35的压力实时反馈给控制中心并记录。
29.位于导向杆311下方的压感组件34包括加热板341、隔热板342、平衡板343,加热板341位于下方,并通过隔热板342与上方的平衡板343连接并形成整体(避免加热板341加热时,热传导的作用导致平衡板343)会出现受热变形,影响整体的受压情况,为了便于控温,加热板341通过电加热方式对压头35整体进行加热,高效便捷。同时平衡板343所在的上端面设置有平衡调节阀3431,平衡调节阀3431分别设置在平衡板343所在的侧边位置,通过平衡调节阀3431用于对平衡板343进行水平度调节,保持压头35下压时的水平度始终保持一
致。
30.压头35设置有若干组(此时的压头数量根据位于载具101上的实际承载的贴盖基板数量决定),并置于block板350所在的下端面,并保持压头35所在的下端面整体保持水平平衡;block板350整体嵌装在压感组件34的加热板341下端面上,通过加热板341的加热传导带动block板350的传导,而此时block板350再将热量传递给压头35,以便实现对压头35的升温作业,可以根据需要,将block板350携带压头35整体从压感组件34上脱离,并可随时更换。
31.如图8、图9所示,block板350所在的下端面竖直方向设置有若干组销钉351,使销钉351对压头35形成外周的包围,同时销钉351向下伸出的高度大于压头35本身的厚度。
32.使block板350与流水带机构2上的载台101接触时,销钉351对载台101整体产生向下的挤压压力,并同步操作顶升模块5的顶升实现位于载台101上的贴盖基板向上抬升,直至压头35与贴盖基板的上端面接触。
33.销钉351位于block板350所连接的端部设置有减震弹簧件352,使销钉351受压时同步实现收缩,脱离时同步实现回弹。正常不受压情况下,销钉351向下伸出的高度大于压头35本身的厚度;销钉351位于压感组件34所连接的端部设置有减震弹簧件352,使销钉351受压时同步实现缓慢回弹,避免压头35位置直接与载台101上的贴盖基板接触造成的挤压损坏,当液压压合模组3抬升后,销钉351复位回弹为下一个工序压合做准备。
34.当压感组件34与流水带机构2上的载台101接触时,销钉351对载台101所在的上表面整体产生向下的缓慢压力(即对载台101整体向下挤压),并同步实现位于载台101上的贴盖基板向上抬升(由于载台101与贴盖基板之间相互分离,实现了载台101与贴盖基板之间的相对脱离),直至压头35与贴盖基板的上端面接触。
35.如图10所示,支撑轨道4用于对液压压合模组3的支撑板32进行支撑,同时顶升模块5位于支撑轨道4所在的下方位置,支撑轨道4通过中部的隔板分为多组,每组隔板区域上方均设置一组液压压合模组3(同时位于液压压合模组3所在下方位置对应设置一组流水带机构2),液压压合模组3的整体置于支撑轨道4所在的上部,支撑轨道4所在的承载侧边对称设置有多组调平板41,每组调平板41均独立调平,此时位于每组液压压合模组3所在中部的支撑板32承载在调平板41上(将液压组件31与压感组件34隔离成上下两个部分,但不影响液压组件31下压时对压感组件34的压力),通过支撑板32与调平板41相互贴合,以调整液压压合模组3整体水平稳定度,保证位于压感组件34下端面压合时的水平精度。
36.如图11所示,每组顶升模块5均位于液压压合模组3所在的正下方位置,可根据需要设置有多组同步工作,提高了保压压合速率,顶升模块5包括伺服电机51、丝杆组件52(多段式的丝杆组件52通过中间的联轴器实现连接传动)、顶升面板53,伺服电机51通过丝杆组件52连通在顶升面板53上,通过顶升面板53从流水带机构2所在的载台101上将阵列分布的贴盖基板顶升。同时位于液压压合模组3上的压头35向下对贴盖基板进行压合,此时的贴盖基板所在的上下两面分别通过液压压合模组3以及顶升模块5进行压合的同时同步实现挤压,保证贴盖基板保压的压力以及保压温度。
37.下料检验模组6采用的结构与上料检验模组1所采用的结构相同(即包括下料接驳单元和下料检测单元,通过下料接驳单元对载有贴盖基板保压后的载台101转运至下料检测单元上),并对载台101上完成保压工序的贴盖基板进行视觉检测(主要检测贴盖基板保
压完成时是否出现漏压或压合损坏的情况)后,检测合格后再转运至下一个工序。
38.基于基板保压的液压式保压工装的保压系统,包括以下步骤:s1、通过上料检验模组1将贴盖基板的载台101进行视觉检测,检测合格后转运至流水带机构2上(上料检验模组1的工作原理参照上述描述)。
39.s2、通过流水带机构2的传送组件22将载台101转运至液压压合模组3所在的下方,并受到位于前端部限位组件221的限位,随后后端部的限位组件221同步抬升并限位,与此同时,通过定位组件211从侧边对载台101进行限位,实现载台101四个方向的位置固定限位(此时贴盖基板为阵列分布,并与压头35一一对应)。
40.s3、首先将控制顶升模块5向上顶升,并使得顶升面板53从载台101所在的底部对贴盖基板进行接触式抬升;与此同时,位于载台101上方的液压压合模组3开始工作:液压组件31下压,使下端部的压力传感器33同步感应受压压力,当多数压力传感器33达到平衡后即可实现位于下方的压感组件34受压均匀。
41.且此时block板350下端面沿竖直方向设置有若干组销钉351,销钉351所在的连接处设置有减震弹簧件352,正常不受压情况下,销钉351向下伸出的高度大于压头35本身的厚度(可以起到对压头35周边的保护作用避免与载台101发生碰撞),当压感组件34受压缓慢下降时,销钉351首先接触位于流水带机构2上的载台101,随后由于销钉351持续受力,会产生向回收缩的反作用力,直至压头35接触贴盖基板的上表面并到达指定压力,同时位于压感组件34上的加热板341对压头35加热到指定温度,并通过热传导作用传递给贴盖基板的上表面,使其达到指定温度,此时位于贴盖基板的上下两个端面均受到挤压(其中上端面的压力可达到1000kg,可满足众多基板的保压压力需要),保证了贴盖基板时的保压温度和保压压力。
42.由于液压压合模组3设置有多组,并且其保压时需要一定时间,因此当其中一组保压时,不影响由流水带机构2传送载台101至另一组液压压合模组3上,且保压完成后每组液压压合模组3均可独立实现传送至下料模组6上(互不干扰),因此在保压时间内,可同时实现多组载台101上的贴盖基板保压工序,大大提高了对于贴盖基板的保压效率。
43.s4、通过流水带机构2将完成保压的贴盖基板及载台101整体转移至下料检验模组6上,通过下料检验模组6将贴盖基板重新检测后,检测合格后,再转运至下一个工序。
44.以上显示和描述了本发明的基本原理、主要特征和本发明的优点。本行业的技术人员应该了解,本发明不受上述实施例的限制,上述实施例和说明书中描述的只是说明本发明的原理,在不脱离本发明精神和范围的前提下,本发明还会有各种变化和改进,这些变化和改进都落入要求保护的本发明范围内。